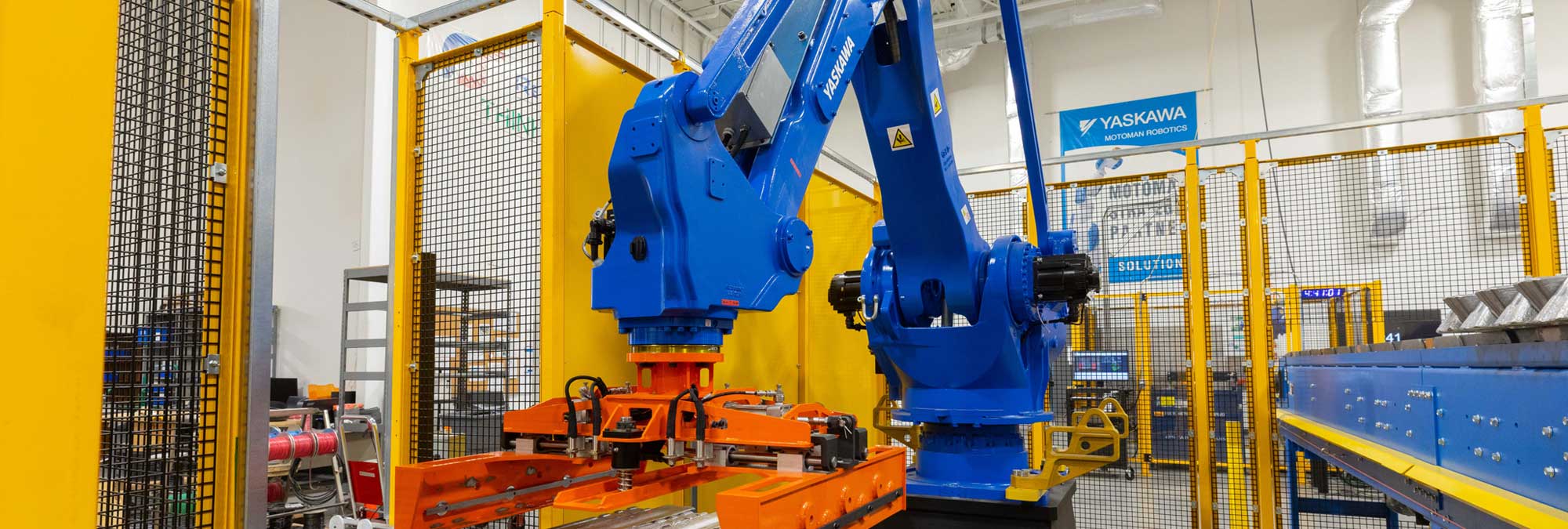
Robotics & Automation
Ready Systems is a preferred supplier of custom automation equipment, assembly lines utilized in manufacturing, palletizing systems, material handling systems, overhead conveyor lines and robot integration.
Robotics
Robot Palletizing Systems
Robotic palletizers are widely used in various industries today for automating the process of palletizing goods, which involves arranging products onto pallets for storage, transportation, or shipment. Ready Systems palletizers offer efficiency, accuracy, and flexibility in handling different types of products and palletizing patterns. In addition Ready Systems offers customized solutions tailored to specific industry requirements. These solutions may involve integrating robots with conveyor systems, vision systems for product recognition, and software for optimizing palletizing patterns and workflows.
Robotic Torque Cells
Robotic cells are custom manufactured for the torquing of safety critical and non-critical bolts in the automotive seating industry. The robot cells are typically fitted with Atlas Copco torque tools and equipment with the compliant torque gun mounted to the robot EOAT. The cell utilizes spatial positioning to ensure the correct bolt is torqued in the correct order to the proper angle and torque. The torque data from each bolt is easily transferred to your MES system for quality control and data tracking. The cells can be customized to torque marriage bolts, seal belt bolts, pretensioners, and seat pan bolts to name a few.
Robotic Seat Offload Cells
Robotic off-load cells are utilized mainly in the seat manufacturing industry. The robot cells utilize a custom EOAT for each seat and application. The seat is robotically transferred from the assembly line to the shipping pallet system. In conjunction with the PLC, the robot will ensure the seats are properly placed on the shipping pallet conveyor to establish the seats are in the proper order for the JIT tier one supplier.
Robotic Bin Picking
Robotic bin picking is a technology used to automate the process of picking parts from bins, pallets or containers. It involves robots equipped with sensors, vision cameras, and specialized software c/w sophisticated algorithms to identify and grasp items accurately and efficiently. This technology has gained significant traction to streamline production processes and improve productivity. Ready Systems robotic bin picking automates the tedious and labor-intensive task of picking parts resulting in faster cycle times and increased throughput. By eliminating manual handling, it reduces the risk of errors and ensures consistent performance, thereby improving overall production efficiency.
Robotic Steam Cells
Ready Systems is also a preferred supplier of Robotic steam cells specifically built for the automotive seating industry. These cells utilize a custom manufactured steam head in conjunction with a VEIT brand generator steamer. Together the robot and steam head are programmed to methodically steam the seat for the removal of wrinkles.
Robotic Machine Tending
Ready Systems has provided many systems to assist you. Typically this includes robots to transfer parts through manufacturing and stamping processes. A few robots work in tandem to pick parts from infeed conveyors and pass them sequentially through the various machines. Vision equipment is integrated with the robot to initially pick parts in the correct orientation and hold this orientation throughout the process.
Vision Systems
Robotic Vision
While using robotic systems helps with general efficiency and productivity of an assembly plant, there are additional benefits that accompany the implementation of a vision system with that robot.
The vision system allows the Robots to be more precise and productive. Rather than requiring a stack of parts to be perfectly placed in alignment and orientation – a vision system can enable a robot to quickly pick the correct part out of a bin of assorted products. This requires far less time to prepare the parts for installation into the assembly process.
Vision systems allow robots to have greater flexibility as well. A robot can identify where on the product it needs to complete its operation based on sight, rather than requiring a specific part placement. This adaptability allows the assembly process to move quicker without being bogged down by manual part placements.
Vision systems also offer greater quality control. When used for analyzing an object, a camera can magnify an image, allowing the robot controls to determine imperfections that would otherwise go unnoticed by the human eye.
Vision in Material Handling
The Vision equipment can also be fixed mounted onto your material handling equipment system as well. They will help analyze inbound parts, or to verify if a screw is missing on an assembly.
Some of our Vision applications include: Defect Detection; Vision Measurement; Vision Inspection Systems; Counting and Identification; Advanced Data Acquisition.
Vision Systems increase the flexibility during the introduction of new part styles/models. They only require additional programming and don’t require additional vision hardware, versus replacing the mechanical solutions used to locate your part.
Vision equipment allows for a quick and easy setup. Mount a single camera with a gigabit Ethernet cable attached to the vision controller.
Ready Systems is more than familiar with IRVision; Cognex; Keyence; and OnRobot vision systems and equipment
Assembly Lines
Twin Strand Pallet Based Assembly Lines
Ready Systems is a leading supplier of twin strand assembly lines. These U.S. manufactured all aluminum pallet-based assembly lines are the industry standard for assembly lines. From single level to over and under configurations, these systems provide not only the unique solutions you demand today, they also have the ability to be easily reconfigured for future programs without the large capital reinvestment of other systems.
AGC – Automated Guided Carts
Ready System offers self-guided industrial vehicles or carts that allow you to significantly optimize your production flow without major investment. Our AGC’s move intelligently and autonomously. An ideal solution to labour shortages, they are reliable, safe and require little maintenance.
AGCs can evolve and change function over time. More flexible than traditional equipment, AGV and AGC’s can be used in restricted spaces and easily integrated into existing production lines. What’s more, you can adjust its travel routes in real time.
Material Handling / Conveyor Systems
Overhead Transfer and Buffer Conveyor Systems
Overhead Power & Free Conveyor systems are typically used to automatically transport and buffer WIP parts between one robot assembly cell and another cell, sometimes on the other side of the factory. Standard overhead Power & Free Conveyor components are used within a custom layout to help ease costing. Custom product Carriers are manufactured to integrate with the robot loading & unloading of parts to and from the line.
Over & Under Tote Exchange Systems
Our over and under tote exchange systems provide a multiple container feeding system for assembly lines and work cells. These systems have a smaller foot print than a side by side system. The containers are placed inbound on the lower level and presented to the operator in an ergonomic pick position. Once filled or parts removed, the empty containers are raised and discharged to the upper level outbound lane. Each Over & Under is manufactured to your container specifications and can handle up to four totes inbound and four totes outbound. These units handle automotive style totes and containers. The system can provide a tote exchange to the operator in as little as 30 seconds.
Side By Side Rack/Tote/Pallet Exchange Systems
Our side-by-side rack exchange systems provide a multiple-container feeding system for assembly lines and work cells. Each system is custom made and can handle up to ten racks inbound and ten racks outbound. The automated conveyor systems can handle shipping racks, contico style tote or containers and pallets. Rack or pallet exchange can be completed in as little as 15 seconds.
Shipping Systems
Shipping Conveyor Systems
Shipping Systems are used to transfer the product from your assembly line to the dock door. The system utilizes conveyor equipment and leading edge PLC controls to ensure the product stays in the proper sequence for loading onto the truck. These systems are manufactured using standard conveyor equipment into your unique layout application. Twin strand aluminum conveyor, chain driven live roller (CDLR) and motor driven roller applications (MDR) are some of the styles currently in use. Each of these conveyor systems allows for the buffering of product between the assembly line and the dock door.